3.鉄
自動車を構成する主な材料である鉄(鉄鋼)は、自動車材料にいちばんに求められた強度信頼性、耐久性、コストなどに応えてきた材料である。市販車は通常の使用状態において、3年または6万kmの品質保証がなされ、パワートレインについては5年10万kmに延長されている。
自動車における鉄鋼材料を見ると、ボディなどに使われる鋼板、エンジン部品などに使われる特殊鋼や鋳鉄などがある。鋼板は自動車において最も使用量が多く、重量比は40%程度である。特殊鋼は高い強度信頼性を有することから、エンジン、駆動、シャシーなど各ユニットの主要構成部品に使われ、17%程度を占め、この比率はあまり変化していない。一方鋳鉄は、シリンダーブロックのアルミ化など軽量化の流れで使用量は減少している。鉄の軽量化には、素材自体の強度を上げることと部材表面に表面処理を施して強くし小型化を図る方向がある。
(1)高張力鋼板
スチールボディ(モノコックボディ)は、全体で350点ほどの部品を4,500点ほどのスポット溶接で組み立てたものであり、各部品は薄鋼板(0.6mm〜1mm)をプレス成形したものであるが、補強のため、一部の部品は厚めの鋼板(2mm程度)も使われる。ボディに使われる薄鋼板は、表面精度の高い冷間圧延鋼板が使われるが、軽量化及び強度向上のため、高張力鋼板(High Tensile Strength Steel、ハイテン)が各所に採用されている。当初の鋼板はプレス成形性そのものが課題であった。その課題を解決し、さらに高強度化と高成形という本来矛盾する課題を克服する材料技術は特筆される。但し、剛性(弾性率)は通常の鋼板も高張力鋼板も同じであるので、高張力鋼板の採用が有効な箇所は、疲労強度や変形強度が要求されるフレーム、ピラー、メンバー類、耐デント性(くぼみなどの変形を防ぐ強度)が要求されるフロントフード、トランクリッドなどの外板パネルなどである。
高張力鋼板は、オイルショックによる自動車の燃費向上のニーズが引き金となり、ボディ軽量化の必要性から採用され始めた。通常の鋼板(引張強度は300MPa程度)より板厚を薄くすることができるため軽くなる。1990年代には440MPa、2000年には590MPa級が一般的となり、超高張力鋼板ともいわれる980MPa、さらに1180MPa、1470MPa級も登場している。
図2には、高張力鋼板と通常の鋼板(SPC、冷間圧延鋼板)の特性を比較したものを示した。焼付け硬化(BH:Bake Hardenability)タイプは、プレス成形時は軟質、つまり降伏強さが低いが、塗装焼付け時の170℃前後の熱によって降伏強さが上昇するもので、特にユニークであり、フロントフードやトランクリッドなどの外板パネルに利用されている。プレス成形性に優れたIF(Interstitial Free)鋼をベースにリンを添加し、深絞り性に優れたタイプもある。複合組織を作り出して強度と加工性を高めたものが複合組織型高張力鋼板(DP、TRIP)である。このタイプは、同じ高強度であっても従来の析出強化タイプに比べ延性が高い。つまりプレス成形性に優れている。
図2●冷間圧延鋼板(SPC)と各種高張力鋼板の機械的特性
注)アルミのデータも併記
出典)高 行男「ポリファイル」47巻、2010年
高張力鋼板は、1990年代、ボディ重量の25〜35%を占めているが、ボディ用鋼板の生産量に占める高張力鋼板の割合(2005年・50%)を見ると、その後も重要性は増している。45%(トヨタ・プリウス、2003年)、さらには57%(トヨタ・アクア、2012年)と言われている。高張力鋼板の使用を36%から53%に拡大した事例(マツダ・デミオ、2007年)を見ると、使用拡大とそれに伴う構造最適化によりボディは22kgの軽量化を達成している。鋼板は440MPa主体から590MPa主体となり、980MPa級のものも採用されている。部材の強度レベルは、衝突時の部品のエネルギー吸収量や部品の成形性・溶接性が考慮され選定されている。
高張力鋼板によりどれくらいボディの軽量化が図れるかをULSAB(Ultra Light Steel Auto Body、1998年)について見ると、25%程度である。ULSABでは高張力鋼板が、定義によるが64〜91%と多用されている。この軽量化の達成において、剛性を確保するボディ構造の最適化や、テーラードブランク、ハイドロフォーミング、レーザー溶接などの加工技術による寄与も大きいことが指摘されている。世界鉄鋼協会では、ULSABに続き、EVやHEVのボディのハイテン化について検討されているが、テーラードブランク、ハイドロフォーミングに加えホットスタンピングとロールフォーミングの加工法が挙げられ、ULSAB以上の軽量化をめざしている。つまり高張力鋼板という素材ばかりでなくその加工法が軽量化を図るうえで重要な役割を果たす。
高張力鋼板はボディの軽量化と衝突安全性向上という本来相反する課題に対処している。つまり衝突安全性を簡便に確保するには補強材を追加すればよいが、重量増となるので、衝突エネルギー吸収能力が高い高張力鋼板の果たす役割は大きい。
(2)特殊鋼
特殊鋼(合金鋼)は、炭素鋼にクロムやニッケルなどいろいろな元素を加えたもので、耐食性や耐熱性など特殊な性質を示す鋼である。使用部品の要求特性に対応するように改良されてきた材料であり、クロムモリブデン鋼などの構造用合金鋼、ステンレス鋼、耐熱鋼、ばね鋼、軸受鋼、快削鋼など多種多様である。歴史を持っており、鉛フリーの快削鋼や清浄度を高めた軸受鋼など、改良され続けられている材料である。比較的馴染みのあるステンレス鋼は、マフラーなどの排気系部品に使われているが、1980年以降1台当たりの使用量が増加している。
構造部材の軽量化の手法は板厚を薄くし、余肉削減が基本であるが、その前提は当然であるが安全性の確保である。軽くするために必要な寸法を減らすと破壊につながる。時間が経過して現れる疲労破壊など厄介な現象もあり、軽量化と安全性のバランスの適正化は大きな課題である。
構造部材は一般的にどの部分であっても軽量化が必要であるが、その重要度は使用部位によってかなり異なる。これは、ある部分(部品)の軽量化がそれ自体の重量軽減にとどまらず,その部分を支えているほかの部分の負担を軽減するからである。例えばコンロッドの軽量化はそれが往復運動部分であるため、エンジン性能の向上ばかりでなくシリンダーブロックやクランクシャフトの負担を軽減し、エンジン全体の軽量化に貢献する。ホンダ・インサイト(1999年)のコンロッドを見ると、表面硬化処理のひとつである浸炭処理をして表面を硬く強くし、小型化することによって30%軽くなっている。鋼の代わりにチタンを採用して軽量化を図っている事例(ホンダ・NSX、1990年)もある。
一方、加工技術の点から見ると、Fe-Cu-C系合金製の粉末鍛造コンロッドの採用例(トヨタ・カムリ、1981年)がある。粉末鍛造とは、焼結体に気孔が在ると強度は低下するので、焼結体を緻密にする処理方法である。自動車焼結部品の端緒は1920年代に開発された焼結含油軸受であるが、この場合は焼結体内部の気孔を利用している。材料の良否は使用目的により異なる。焼結材料(焼結金属)は鋼と競合する材料として期待される。
(3)鋳鉄
鋳鉄は複雑な形状も鋳込むことができ、耐摩耗性や振動吸収性に優れている。ピストン材も当初は鋳鉄で、アルミピストンが登場(1915年)しなければその座を守った材料である。但し、耐熱性、耐摩耗性などの点から、今日でも鋳鉄ピストン、鋳鉄ブロックは使用されている。鋳鉄においても一般的なねずみ鋳鉄、片状黒鉛を持つねずみ鋳鉄のもろさを改善した球状黒鉛鋳鉄、耐酸化性などを改良した高ケイ素球状黒鉛鋳鉄など、鋳鉄自身も改良され採用されている。軽量化の視点で見ると、鋳鉄はアルミばかりでなく鉄という同じ仲間の鋼と競合している。その対象は、クランクシャフト、カムシャフト、排気マニホールドなどである。
4.アルミ
アルミ(Al)の比重は2.7で、鉄の約1/3である。アルミ系材料には、ジュラルミンなど強度の高い合金が多いので、比強度(強度/比重)の高いことが大きな特徴である。金属は鉄と非鉄に大別されるが、非鉄金属材料の代表がアルミであると言える。材料のニックネームとして、鉄が王とすればアルミは女王かと思っている。その主な理由は剛性で、鉄と同程度の強さのアルミでもその剛性は低く、剛性は合金では改善されない。
アルミには鋳造用と展伸用がある。鋳造用アルミには普通鋳造用とダイカスト用があるが、鋳鉄(比重7.1)に比較して軽量であること、鋳造性が良好なことから、軽量化が要求される自動車部品への使用量が増大し、重量比率で約7%弱である。エンジンやトランスミッション部位では、80%近くが鋳物やダイカスト合金が使われている。
一方、展伸用アルミは、加工用Al合金(圧延、鍛造、押出し、引抜きなどで加工される材料)と高力Al合金、あるいは非熱処理型合金(3000、4000、5000系)と熱処理型合金(2000、6000、7000系)とに分類されるが、5000系と6000系がボディに使われている。2000系と7000系のアルミが高力Al合金であるジュラルミンである。7000系のジュラルミンは超々ジュラルミンとも称され日本で開発された。またアルミの表面処理であるアルマイト処理も日本で開発され、アルミは日本と関係が深い材料である。軽量化の視点で事例を見るとき、新幹線車両(1982年、200系車両)がスチールのアルミ化で9トンから7.5トンになることを考えると、材料置換の効果がイメージしやすい。
(1)アルミボディ
アルミは従来から鋳造や鍛造品がエンジンや足回りに使われているが、1986年からボディ(マツダ・RX-7、フロントフード)にも利用され始め、ボディの一部、例えばフロントフード、ルーフ、フェンダー、トランクリッドにアルミを採用する傾向が増加している。軽量化ばかりでなく、運動性能の向上に効果があるためである。軽量化の事例(トヨタ・プリウス、2003年)を見ると、フロントフードで3.2kg、バックドアで6kg程度、ルーフの事例(三菱・ランサーエボリュ−ション、2005年)では4kgくらい軽量になる。
アルミによりどれくらいボディの軽量化が図れるかをオールアルミボディのホンダ・NSX(1990年)について見ると、同サイズのスチールボディに比べ40%程度の軽量化である。この軽量割合は、アウディ・A8(1994年)では約40%、アウディ・A2(1999年)では約43%なので、アルミボディの重さはスチールボディの6割くらいになると言える。
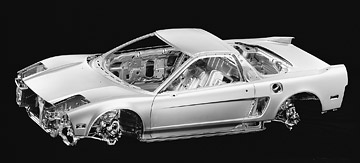
オールアルミボディのNSX
写真提供:本田技研工業
NSXはアルミを多用したスポーツカーで、軽量化を運動性能の向上に活用するのが当初の目的である。一般乗用車の7.2%に対し31.3%のアルミの活用によりボディだけで140kg、総重量で約200kgの軽量化を達成している。アルミは鉄(比重7.9)の1/3程度の軽さであるが、剛性(弾性率)を見ると、アルミ(70GPa)は鉄(206GPa)の1/3である。軽量化の一例としてルーフを考えると、べこつき感を示す張り剛性は弾性率が関係するので、同一形状ではアルミの厚さは鉄の1.4倍必要である。それでもアルミは軽い。NSXの事例では、アルミルーフ(厚さ1.2mm、重さ2.6kg)は、スチールルーフ(厚さ0.85mm、重さ5.4kg)の半分くらいの重さである。
一般にアルミは加工性が良いと言われるが、それは押し出しや圧延加工である。アルミ板材のプレス成形は鋼板と同様に行うが、伸びが鋼板(SPC)の65%程度で成形性は劣る(図2参照)。コストも高く、板金修理が難しい問題などもある。ハイテンを含むスチール同士の接合ではスポット溶接が主流であるが、アルミの場合には電気伝導、熱伝導が良いため大電流短時間通電が必要となり、問題となる。上述のアウディ・A8ではスポット溶接とMIG溶接、リベット止めなどが接合に使用されているが、アウディ・A2ではスポット溶接に代わりレーザー溶接、そしてMIG溶接とリベット止めである。アルミの接合方法にもいくつかのものが登場しているが、FSW(Friction Stir Welding、摩擦攪拌接合)がユニークと思っている。この方法は溶接でなく塑性流動によって接合する。1991年に誕生し、新幹線の車両に採用されたが、自動車にも適用されている。
スチールボディにアルミルーフなど、アルミとスチールの異材接合には、電食が発生しないように、リベット(三菱・アウトランダー、2005年)や接着剤(BMW7シリーズ、2009年)が採用される。接着の場合、ボディの鉄とアルミの熱膨張率(線膨張係数)は異なるので、温度による変形の違いを接着剤が吸収する必要がある。長期の実走行における接着機能の耐久性が注目される。
(2)エンジン
エンジンはボディに次いで重量割合が大きい。エンジン重量の1/4程度を占めるシリンダーブロックのアルミ化が1980年代に始まり今日に至っているが、興味ある軽量化事例にアルミとマグネシウム(比重1.74)を複合したシリンダーブロック(BMW・630i、2004年)がある。
ブロックのアルミ化においてライナーは鋳鉄が使用されるが、鋳鉄ライナーの代わりにFRM製スリーブの採用例(ホンダ・プレリュード、1991年)がある。アルミと繊維(アルミナ繊維と炭素繊維)を複合することによってアルミの弱点である耐摩耗性を強化し、ボア間の肉厚の薄肉化を図ることによりエンジンのコンパクト化、軽量化に貢献している。一方ライナーレスアルミシリンダーも登場している。
マトリックス(母材)に軽量のアルミ合金などを用い、繊維強化したものが繊維強化金属(FRM:Fiber Reinforced Metal)である。FRMが初めて自動車材料として使用されたのは、1980年代で、ディーゼルエンジンのピストン耐摩環である。アルミの複合材料としてFRMの活躍が期待される。
(3)サスペンション
サスペンションの重量割合もエンジンに次いで大きい。アルミサスペンションパーツの軽量化事例(トヨタ・セルシオ、2000年)を見ると、鋼材からアルミ鍛造で、ナックルは4.8kgから2.8kg、アッパアームは2kgから1kgとなり、鋳鉄のキャリアをアルミ鋳物にすると5kgから3kgとなっている。課題もあるが、オールアルミサスペンションに向けて進んでいる。

前へ 2/7 次へ  |